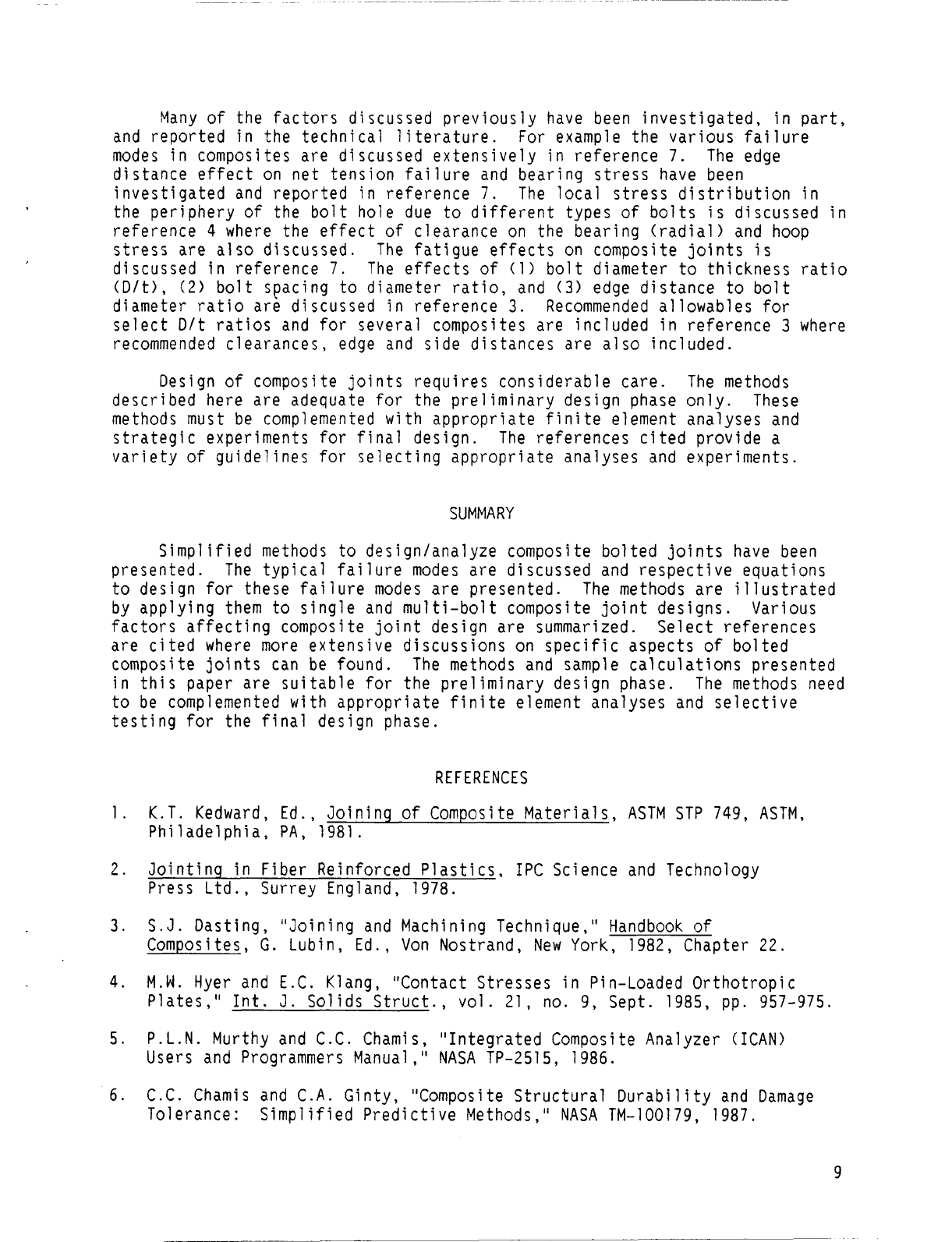
Many
of
the factors discussed previously have been investigated, in part,
and reported in the technical literature. For example the various failure
modes in composites are discussed extensively in reference
7.
The edge
distance effect on net tension failure and bearing stress have been
investigated and reported
in
reference
7.
The local stress distribution in
the periphery
of
the bolt hole due to different types
of
bolts is discussed in
reference
4
where the effect
of
clearance on the bearing (radial) and hoop
stress are also discussed. The fatigue effects on composite joints
is
discussed in reference
7.
The effects
of
(1)
bolt diameter to thickness ratio
(D/t>,
(2)
bolt spacing to diameter ratio, and
(3)
edge distance to bolt
diameter ratio are discussed in reference
3.
Recommended allowables for
select D/t ratios and for several composites are included in reference
3
where
recommended clearances, edge and side distances are also included.
Design
of
composite joints requires considerable care. The methods
described here are adequate for
the preliminary design phase only. These
methods must be complemented with appropriate finite element analyses and
strategic experiments for final design. The references cited provide a
variety
of
guidelines for selecting appropriate analyses and experiments.
SUMMARY
Simplified methods to designlanalyze composite bolted joints have been
presented. The typical failure modes are discussed and respective equations
to design for these failure modes are presented.
by applying them to single and multi-bolt composite joint designs. Various
factors affecting composite joint design are summarized. Select references
are cited where more extensive discussions on specific aspects
of
bolted
composite joints can be found. The methods and sample calculations presented
in this paper are suitable for the preliminary design phase. The methods need
to be complemented with appropriate finite element analyses and selective
testing for the final design phase.
The methods are illustrated
REFERENCES
1.
K.T. Kedward, Ed., Joining
of
Composite Materials, ASTM STP
749,
ASTM,
Philadelphia, PA, 1981.
2.
Jointing in Fiber Reinforced Plastics, IPC Science and Technology
Press Ltd., Surrey England,
1978.
3.
S.J.
Dasting, "Joining and Machining Technique," Handbook
of
Composites,
G.
Lubin,
Ed.,
Von Nostrand, New York,
1982,
Chapter
22.
4.
M.W. Hyer and E.C. Klang, "Contact Stresses in Pin-Loaded Orthotropic
Plates," Int.
J.
Solids Struct.,
vol.
21,
no.
9,
Sept.
1985,
pp. 957-975.
5.
P.L.N. Murthy and
C.C.
Chamis, "Integrated Composite Analyzer (ICAN)
Users and Programmers Manual," NASA TP-2515, 1986.
6.
C.C.
Chamis and C.A. Ginty, "Composite Structural Durability and Damage
Tolerance: Simplified Predictive Methods," NASA TM-100179, 1987.
9