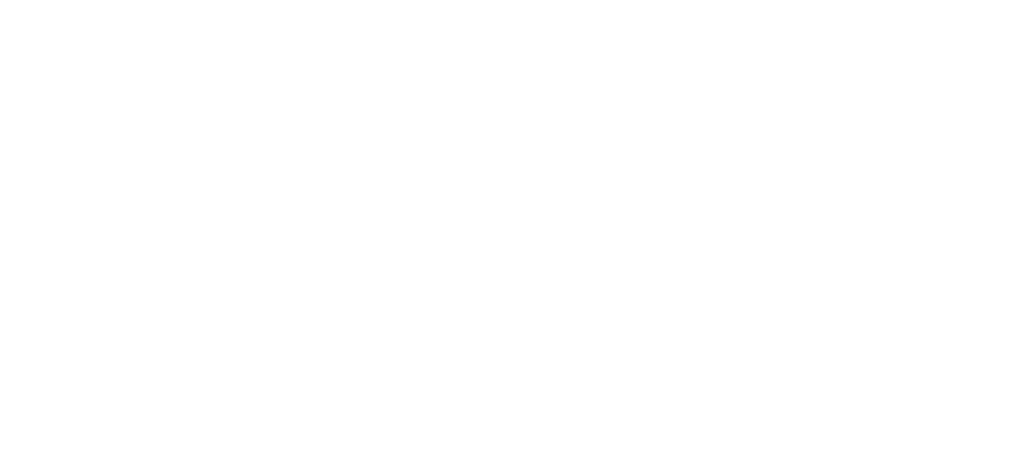
March 2023 Thermal
HIR 2023 version (eps.ieee.org/hir) Chapter 20, Page 36 Heterogeneous Integration Roadmap
Water on a Heated Silicon Surface,” Proceedings of the 2005 ASME Summer Heat Transfer Conference, San Francisco,
CA, USA, July 17-22, 2005
[47] P. Birbarah et al., 2020, Water immersion cooling of high power density electronics,Int. J. Heat Mass Transf., vol. 147, p.
118918, Feb. 2020, doi: 10.1016/j.ijheatmasstransfer.2019.118918.
[48] D. B. Tuckerman and R. F. W. Pease, 1981, High-performance heat sinking for VLSI,” IEEE Electron Device Lett., vol. 2,
no. 5, pp. 126–129, May 1981, doi: 10.1109/EDL.1981.25367.
[49] K. P. Drummond et al., 2018, Characterization of hierarchical manifold microchannel heat sink arrays under simultaneous
background and hotspot heating conditions, Int. J. Heat Mass Transf., vol. 126, pp. 1289–1301, Nov. 2018, doi:
10.1016/j.ijheatmasstransfer.2018.05.127.
[50] A. Bar-Cohen, J. J. Maurer, D. H. Altman, 2017, “Gen3 Embedded Cooling for High Power RF Components”, Keynote
Paper, Proceedings IEEE COMCAS, Tel Aviv, Israel.
[51] Near Junction Thermal Transport (NJTT), DARPA-BAA-11-09, posted Nov. 2010.
[52] Intrachip/Interchip Enhanced Cooling Fundamentals (ICECool Fundamentals), DARPA-BAA-12-50, posted June 2012.
[53] Intrachip/Interchip Enhanced Cooling Applications (ICECool Applications), DARPA-BAA-13-21, posted February 2013.
[54] M. Tyhach, D. Altman, S. Bernstein, R. Korenstein, J.-W. Cho, K. E. Goodson, D. Francis, F. Faili, F. Ejeckam, S.Kim, S.
Graham, "S2-T3: Next generation gallium nitride HEMTs enabled by diamond substrates." In IEEE Lester Eastman
Conference on High Performance Devices (LEC) pp. 1-4 (2014).
[55] J. Pomeroy, M. Bernardoni, A. Sarua, A. Manoi, D.C. Dumka, D.M. Fanning, M. Kuball, "Achieving the best thermal
performance for GaN-on-Diamond," in CSICS (2013).
[56] E. Bozorg-Grayeli, A. Sood, M. Asheghi, V. Gambin, R. Sandhu, T. I. Feygelson, B. B. Pate, K. Hobart, and K. E.
Goodson. "Thermal conduction inhomogeneity of nanocrystalline diamond films by dual-side thermoreflectance." Applied
Physics Letters, Vol. 102, no. 11, pp. 111907 (2013).
[57] J.E. Graebner, S. Jin, G.W. Kammlott, J.A. Herb, C.F. Gardinier. "Large Anisotropic Thermal Conductivity in Synthetic
Diamond Films." Nature, Vol. 359 pp. 401-403, (1992).
[58] A. Bar-Cohen, J.J. Maurer, and A. Sivananthan, Near-Junction Microfluidic Thermal Management of RF Power
Amplifiers, IEEE International Conference on Microwaves, Communications, Antennas, and Electronic Systems
(COMCAS 2015) (Tel Aviv, Israel, 2015).
[59] M. Tyhach, D. Altman, S. Bernstein, "GaN on Diamond Technology: Impact and Challenges of Next Generation GaN,"
presented in ASME InterPACK (2015).
[60] A. Bar-Cohen, J.J. Maurer, J.G. Felbinger, DARPA’s intra/interchip enhanced cooling (ICECool) program, Proceedings of
the Compound Semiconductor Manufacturing Technology Conference (CS MANTECH), (2013) 171-174.
[61] K. P. Drummond, D. Back, M. D. Sinanis, D. B. Janes, D. Peroulis, J. A. Weibel, and S. V. Garimella, A hierarchical
manifold microchannel heat sink array for high-heat-flux two-phase cooling of electronics, International Journal of Heat
and Mass Transfer 117, pp. 319–330, 2018.
[62] K. P. Drummond, D. Back, M. D. Sinanis, D. B. Janes, and D. Peroulis, J. A. Weibel, and S. V. Garimella,
Characterization of hierarchical manifold microchannel heat sink arrays under simultaneous background and hotspot
heating conditions, International Journal of Heat and Mass Transfer 126A, pp. 1289-1301, 2018.
[63] Palko, J.W., Zhang, C., Wilbur, J.D., Dusseault, T.J., Asheghi, M., Goodson, K.E. and Santiago, J.G., 2015, “Approaching
the limits of two-phase boiling heat transfer: High heat flux and low superheat,” Applied Physics Letters, 107(25),
pp.253903.
[64] Jung, K.W., Kharangate, C.R., Lee, H., Palko, J., Zhou, F., Asheghi, M., Dede, E.M., Goodson, K.E., 2019,” Embedded
Cooling with 3D Manifold for Vehicle Power Electronics,” Int. J. Heat Mass Transf. 130, pp. 1108-19.
[65] Ćoso, D., Srinivasan, V., Lu, M.C., Chang, J.Y. and Majumdar, A., 2012. Enhanced heat transfer in biporous wicks in the
thin liquid film evaporation and boiling regimes. Journal of Heat Transfer, 134(10), pp.101501.
[66] Hwang, G.S., Fleming, E., Carne, B., Sharratt, S., Nam, Y., Dussinger, P., Ju, Y.S. and Kaviany, M., 2011. Multi-artery
heat-pipe spreader: Lateral liquid supply,” Int. J. Heat Mass Transf., 54(11-12), pp.233440.
[67] Nam, Y., Sharratt, S., Cha, G. and Ju, Y.S., 2011. Characterization and modeling of the heat transfer performance of
nanostructured Cu micropost wicks. Journal of Heat Transfer, 133(10), pp.101502.
[68] Cai, Q. and Chen, Y.C., 2012, “Investigations of biporous wick structure dryout,” Journal of Heat Transfer, 134(2),
pp.021503.
[69] Semenic, T. and Catton, I., 2009, “Experimental study of biporous wicks for high heat flux applications,” Int. J. Heat Mass
Transf. 52, pp.5113-5121.
[70] Weibel, J.A., Garimella, S.V. and North, M.T., 2010, “Characterization of evaporation and boiling from sintered powder
wicks fed by capillary action,” Int. J. Heat Mass Transf., 53(19-20), pp.4204-4215.
[71] Bae, D.G., Mandel, R.K., Dessiatoun, S.V., Rajgopal, S., Roberts, S.P., Mehregany, M. and Ohadi, M.M., 2017,
”Embedded two-phase cooling of high heat flux electronics on silicon carbide (SiC) using thin-film evaporation and an
enhanced delivery system (FEEDS) manifold-microchannel cooler,” In Thermal and Thermomechanical Phenomena in
Electronic Systems (ITherm), 2017 16th IEEE Intersociety Conference on (pp. 466-472).
[72] Jung, K.W., Jih, E., Iyengar, M., Asheghi, M., Malone, C., Man Prakash, G., Goodson, K.E., 2018, “CFD modeling of
embedded cooling with 3D manifold for vehicle power electronics”, Ongoing work at Stanford.